Distinguish between coefficient method and ratio method applied in calculating product cost
Posted date 08/05/2018
16.450 view
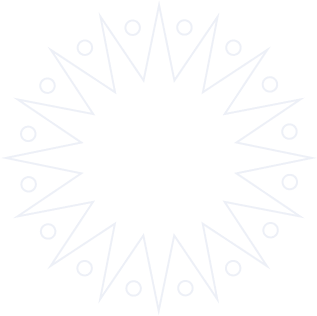
The coefficient method and the ratio method are two costing methods applied in cases where, on the same technological process, in the same production process, many different types of products (many costing objects) are simultaneously completed.
The coefficient method and the ratio method are two costing methods applied in cases where, on the same technological process, in the same production process, many different types of products (many costing objects) are simultaneously completed.
In fact, these are methods of allocating input production costs to costing objects because it is impossible to separate those costs in the production process. Currently, in accounting textbooks, the ratio method is still written sketchily through a formula for calculating the cost ratio, causing the misconception that the ratio method is only different from the coefficient method in that instead of using a conversion coefficient, the cost ratio is used. This article aims to analyze in depth the similarities and differences between the two coefficient and ratio methods in terms of scope, application sequence and illustrate with specific examples.
First of all, let's talk about the scope and application sequence of the coefficient method. The coefficient method is suitable in cases where a business produces one type of product but has different sizes, designs or quality levels. For example, a shoe factory produces shoes of different sizes, a tea factory produces tea with quality levels 1, 2, etc. The application sequence of the coefficient method includes the following steps:
Step 1: Convert different costing objects to the same standard product type through the conversion factor. The conversion factor is usually calculated by comparing the selling prices of different sizes and grades and is stable between different costing periods.
Number of standard products = ∑ Q i H i ; (1)
In which, Q i – Number of products of type (group) i completed in production during the period;
H i – Product coefficient of type (group) i
Step 2: Calculate the standard unit product cost according to the formula:
In fact, these are methods of allocating input production costs to costing objects because it is impossible to separate those costs in the production process. Currently, in accounting textbooks, the ratio method is still written sketchily through a formula for calculating the cost ratio, causing the misconception that the ratio method is only different from the coefficient method in that instead of using a conversion coefficient, the cost ratio is used. This article aims to analyze in depth the similarities and differences between the two coefficient and ratio methods in terms of scope, application sequence and illustrate with specific examples.
First of all, let's talk about the scope and application sequence of the coefficient method. The coefficient method is suitable in cases where a business produces one type of product but has different sizes, designs or quality levels. For example, a shoe factory produces shoes of different sizes, a tea factory produces tea with quality levels 1, 2, etc. The application sequence of the coefficient method includes the following steps:
Step 1: Convert different costing objects to the same standard product type through the conversion factor. The conversion factor is usually calculated by comparing the selling prices of different sizes and grades and is stable between different costing periods.
Number of standard products = ∑ Q i H i ; (1)
In which, Q i – Number of products of type (group) i completed in production during the period;
H i – Product coefficient of type (group) i
Step 2: Calculate the standard unit product cost according to the formula:
Unit price standard products | = | Actual total cost | (2) |
Number of products that meet standards |
In there,
Actual total cost | = | Unfinished products at the beginning of the period | + | Production costs during the period | - | End of period unfinished products | ; (3) |
Step 3: Calculate unit cost of each type (group) of product:
Unit cost of product type i = Unit cost of standard product x H i ; (4)
Step 4: Calculate the total cost of each type (group) of product:
Total cost of product type i = Output of product type ix Unit cost of product type i ; (5)
The ratio method is applied in the case of the same technological process, on the basis of the same type of raw materials to produce many different types of products. For example: a leather factory produces different products from leather such as leather wallets, belts, leather shoes, leather bags... These products will have different cost structures (proportions of cost items in the cost price). For example: leather wallets compared to leather bags will cost less in leather materials but labor costs may be higher... Therefore, to allocate costs to different types of products, people rely on the consumption rate or standard cost (or planned cost) of these types of products. The cost calculation sequence is as follows:
Step 1: Calculate the total standard (or planned) cost of actual production output according to each cost item and then summarize according to the formula:
Total standard cost of actual quantity = ∑ Q i Z i ; (6)
In which, Q i – Production output of product i completed in the period
Z i – standard cost (KH) of product i unit
Step 2: Calculate the cost ratios of each cost item in actual production output and then summarize according to the formula:
Proportion cost | = | Actual total cost | (7) |
Total standard cost (KH) calculated for actual output |
In which, the actual total cost is calculated according to formula (3)
Step 2: Create a table to calculate the actual cost of each product type, including:
Actual cost per unit SPi = Standard cost per unit SPi x Cost ratio; (8)
Total actual cost of SP i = Quantity of SPi x Actual cost of SPi unit; (9)
Note that formulas (7), (8), (9) are calculated separately for each cost item because each item has a different cost ratio.
Through the above analysis, we can draw the following similarities between the coefficient method and the norm method:
- The two methods of calculating cost by coefficient and by standard are both commonly applied in the production of consumer goods with simple technological processes and diverse production items, but are suitable for different production organization situations and production items.
- The total cost of all actual output is calculated using the simple (direct) method according to formula (2).
- Both methods must calculate the cost allocation criteria as a conversion factor or cost ratio.
- When calculating the cost for each cost object (each type of product), calculate the unit cost first and then multiply by the number of completed products to calculate the total cost.
However, going into details, there are also many differences between the two methods through the following comparison table:
Coefficient method | Ratio method |
Applicable in case of production same item but different size or different quality levels. | Applicable in case of production Many items with structured payments different expense items. |
Conversion factor calculated by comparison selling price of pricing objects different | Price ratio calculated by comparison Actual total cost vs total cost standard (or plan) of output actual by item. |
The conversion factor applies uniformly to all cost items of a cost object | Cost ratio of each item Prices are different but apply uniformly. best for cost objects. |
The conversion factor applies uniformly to different costing periods, no need to be recalculated (unless there is a price change) sell). | The cost ratio will vary between periods. costing depends on change change in product output structure Each cost calculation period must be recalculated. |
There are standard products with the system. conversion factor equal to 1.0 | No standard products |
The product groups all have the same Same and identical cost structure with the structure of total cost reality. | Products without cost structure same (due to price determination) Their levels have a different structure. each other…) |
Application order: - Calculate product conversion factors - Convert all output standard output product - Calculate total cost and cost price standard product unit - Calculate unit cost of each type products on a unit cost basis Standard SP and conversion factor. - Calculate total cost of each type products on a unit cost basis and production output | Application order: - Calculate total cost plan (or norm) of actual output by item - Calculate the cost ratios of each item - Calculate unit cost of products products on the basis of standard cost and price ratios - Calculate total cost of each type products on a unit cost basis and production output |
Just create a cost sheet common to all products (can be combined) Okay) | Each type of product must have its own price calculation table. (difficult to combine into one table) calculate but still clearly calculate). |
The following is an example illustrating the coefficient method and the costing ratio method mentioned above with the same production output and the same total actual cost of the entire production output in the period to easily see the difference between these two methods:
Suppose that at a company X, in the same period, during the same production process, on the same technological process, 2,000 units of product A, 1,200 units of product B and 700 units of product C were produced. The total actual cost of the entire actual output calculated (according to formula 1) is: 184,000,000 VND, of which direct material cost is 106,000,000 VND (accounting for 57.6% of the cost), direct labor cost is 42,000,000 VND (accounting for 22.8% of the cost), general production cost is 36,000,000 VND (accounting for 19.6%).
Case 1: Calculate the total cost and unit cost of products A, B, C using the coefficient method , knowing that H a = 1, H b = 1.2 and H c = 0.8.
Then, we have standard product output equal to:
(2,000 SPA x 1) + (1,200 SPB x 1.2) + (700 SPC x 0.8) = 4,000 standard SP
Based on the total cost of all actual output, output of each type of product and conversion coefficients, it is possible to create a Cost Calculation Table for product types A, B, C (see Table 1).
In which, the standard product unit cost is calculated according to formula (2), which is the total cost divided by 4,000 standard products, the unit cost of products A, B, C is calculated according to formula (4), which is the standard product unit cost multiplied by the conversion factor. The total cost of products A, B, C is calculated according to formula (5), which is the output of each product type multiplied by the corresponding product unit cost. Formulas (2), (4), (5) must be calculated according to each cost item (shown in the rows of the Cost Calculation Table). The total cost of all products must be equal to the total cost of the standard product (can be compared directly on the Cost Calculation Table).
Through the calculation results, it can be seen that because all cost items are allocated to product types according to the same coefficient, all product types have the same cost structure and are similar to standard products or to the total cost of the entire actual output. It can be compared figuratively that the cost of these product types is like similar triangles with different sizes (three dimensions of the triangle).
Case 2: Calculate the cost price of products A, B, C using the ratio method , knowing that the standard unit cost price of products A, B, C is as follows: (Unit: 1,000 VND)
Item | Product A | Product B | Product C |
Material cost TT | 31 | 50 | 15 |
Research and Development Cost | 4 | 9 | 16 |
General production costs | 7.5 | 15 | 10 |
Add | 42.5 | 74 | 41 |
Table 1: COST CALCULATOR OF PRODUCTS A, B, C
(By coefficient method)
Period………………………
Output: 2,000 SPA, 1,200 SPB, 700 SPC, standard 4,000 SP
Unit: 1,000 VND
(By coefficient method)
Period………………………
Output: 2,000 SPA, 1,200 SPB, 700 SPC, standard 4,000 SP
Unit: 1,000 VND
Item cost | Standard products | Product A (H a = 1.0) | Product B (H b = 1.2) | Product C (H c = 0.8) | ||||
Total cost | Unit price | Unit price | Total cost | Unit price | Total cost | Unit price | Total cost | |
A | 1 | 2 | 3 | 4 | 5 | 6 | 7 | 8 |
Material cost TT | 106,000 | 26.5 | 26.5 | 53,000 | 31.8 | 38,160 | 21.2 | 14,840 |
Research and Development Cost | 42,000 | 10.5 | 10.5 | 21,000 | 12.6 | 15,120 | 8.4 | 5,880 |
General production costs | 36,000 | 9.0 | 9.0 | 18,000 | 10.8 | 12,960 | 7.2 | 5,040 |
Add | 184,000 | 46.0 | 46.0 | 92,000 | 55.2 | 66,240 | 36.8 | 25,760 |
Step 1: Calculate the cost ratio for each item.
- Cost ratio of raw material cost item:
% of cost (k/m of material cost) | = | 106,000 x 100% | = | 80 % |
(2,000A x 31) + (1,200B x 50) + (700C x 15) |
- Cost ratio of direct labor cost item:
% of cost (k/m of NC cost) | = | 42,000 x 100% | = | 140 % |
(2,000A x 4) + (1,200B x 9) + (700C x 16) |
- Cost ratio of general manufacturing cost item:
% of cost (k/m of general production costs) | = | 36,000 x 100% | = | 90 % |
(2,000A x 7.5) + (1,200B x 15) + (700C x 10) |
Step 2: Create costing tables for each product type A, B, C (see Table 2)
In table 2, column 1 data is given, column 2 data is calculated above, column 3 data = column 1 x column 2, column 4 data = column 3 x 2,000 (SPA output).
Through the calculation results, it is easy to see that the actual cost structure of each type of product depends on the standard cost structure and cost ratios in the period, and these ratios depend on the production output structure in the period, so they will change between periods. There is absolutely no "similarity" as in the case of applying the coefficient method.
Table 2: PRODUCT COST CALCULATOR A
(By ratio method)
Period……………..
Production: 2,000 units
Unit: 1,000 VND
In table 2, column 1 data is given, column 2 data is calculated above, column 3 data = column 1 x column 2, column 4 data = column 3 x 2,000 (SPA output).
Through the calculation results, it is easy to see that the actual cost structure of each type of product depends on the standard cost structure and cost ratios in the period, and these ratios depend on the production output structure in the period, so they will change between periods. There is absolutely no "similarity" as in the case of applying the coefficient method.
Table 2: PRODUCT COST CALCULATOR A
(By ratio method)
Period……………..
Production: 2,000 units
Unit: 1,000 VND
Item | Standard price of 1 product | % of cost | Actual price of 1 product | Total cost |
A | 1 | 2 | 3 | 4 |
Material cost TT | 31.0 | 80% | 24.8 | 49,600 |
Research and Development Cost | 4.0 | 140% | 5.6 | 11,200 |
General production costs | 7.5 | 90% | 6.75 | 13,500 |
Add | 42.5 | 37.15 | 74,300 |
Following the above logic, create a similar Table for products B and C (the cost ratio column data of the Tables remains the same). Then, add up the total cost of all 3 types of products A, B, C (row plus column 4) - the added number must match the total cost of the entire actual output (in this case, 184,000,000 VND). If during the calculation process, an odd number must be rounded, the rounding must be done so that when adding up the total cost of all types of products, it must match the total actual cost of the entire actual output.
Thus, if the coefficient method applies 1 coefficient to all 3 items of a costing object but does not coincide with the coefficient of another object, the ratio method requires each costing item to have its own ratio but these ratios are applied to the same item of different costing objects.
Latest article
View all Posts
Related articles
See all related Articles